The flywheel had spun slightly. So I have now taken apart and reassembled with a new key, lapping the flywheel well and torquing it down with the rope in the bore trick to lock the crank, and the special clutch drive tool which I bought for the job.
The mower was then running OK, but was difficult to start without pouring a little petrol into the carb – which pointed to the choke. With the air filter off, I sprayed some GT85 into the bowden cable and sprayed carb cleaner into the carb, and wiggled the control lever back and forward to make sure that the choke butterfly was flapping as it should do. It wasn’t at first, but was after a bit of attention. With that done and checking that the bowden cable was clamped in the right place, the mower starts, and I’ve been able to do some mowing. I’m really pleased – the machine is just what I need and I hope I can keep it going for a while now.
I need to make a few parts that are missing – might anyone be able to send me close up photos of them?
They are the wing nut that adjusts the height at the back, and the collar beneath it, and also the front wheel hub caps.
thanks
Matt
Attachments:
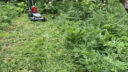